Innovation in the world of business often demands bold moves that challenge the status quo. While traditional methods have long dominated industries like cold storage, growing demands for energy efficiency, sustainability, and operational flexibility have driven the need for new solutions. One such solution, Ultra’s i-Air, is transforming the way cold storage refrigeration operates, offering energy-efficient, environmentally responsible, and highly adaptable cooling systems. This case study explores how Dale Brothers, a Telford-based logistics company, took the leap into innovative cold storage technology with i-Air, overcoming challenges to achieve substantial energy savings, operational efficiency, and environmental benefits.
The Need for Innovation in Cold Storage:
Cold storage has traditionally relied on conventional refrigeration systems with inherent high energy consumption, frequent maintenance needs, and environmental concerns. These systems, while effective, can be costly to operate and contribute significantly to carbon emissions due to their reliance on high-GWP (Global Warming Potential) refrigerants and inefficient energy use.
In the face of these challenges, businesses in the cold storage sector are increasingly looking for more sustainable alternatives. Dale Brothers, a well-established logistics company, faced the challenge of constructing its first refrigerated warehouse. This step required not only a rethinking of its operational model but also a careful consideration of advanced refrigeration systems. i-Air emerged as the ideal solution, offering a more efficient, flexible, and environmentally friendly approach to cold store refrigeration.
i-Air: A Game-Changing Technology for Cold Storage
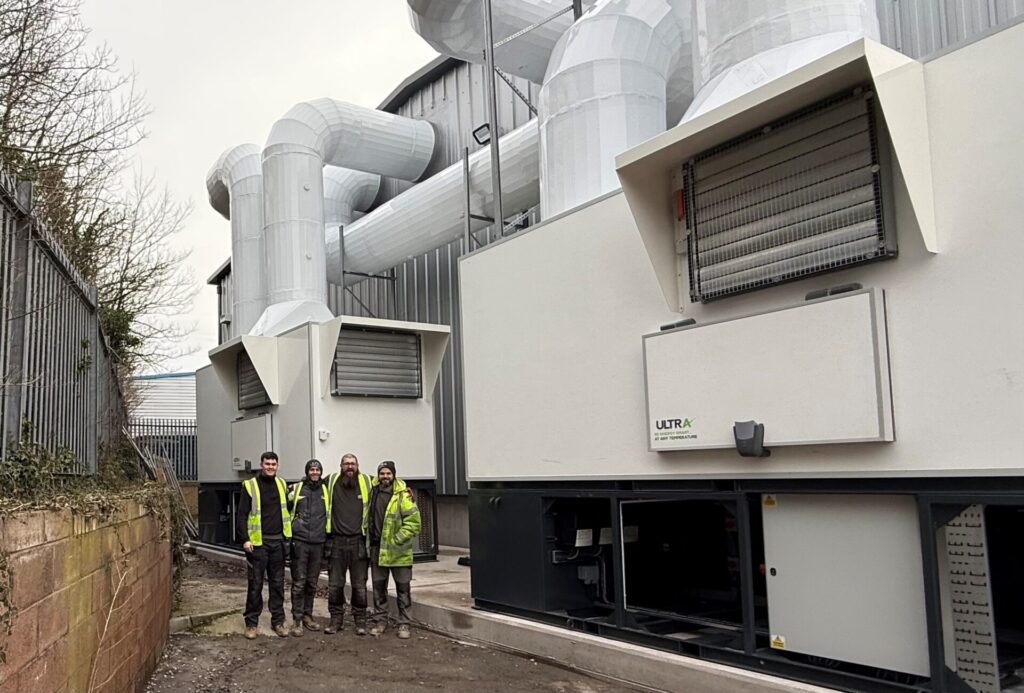
i-Air is an innovative refrigeration system that departs from traditional approaches by utilising a remote refrigeration unit paired with Air Handling Units (AHUs) to deliver cooled air via ducts. One of the key advantages of i-Air is its ability to deliver ‘free cooling’—using outside air to refrigerate the cold store when ambient conditions allow. This reduces energy consumption significantly, leading to substantial savings compared to conventional refrigeration methods.
Key advantages of i-Air include:
- Energy Optimisation: i-Air adjusts its operation based on internal and external conditions, determining whether to recirculate or expel air for maximum energy efficiency, so minimising energy costs.
- Increased Storage Space: By eliminating the need for bulky evaporators within the cold store, i-Air frees up valuable space, which can be used for additional racking and storage. This project created around 25% more usable storage space within the confines of the building.
- Ease of Maintenance: Unlike traditional systems with high-mounted evaporators, i-Air’s design makes maintenance tasks safer, more accessible, and less time-consuming, improving operational uptime.
- Scaleable: there is no limit to the size of cold store that can benefit from i-Air; in fact, the larger the building the greater the benefits.
- Real-Time Monitoring and Analysis: i-Air continuously monitors critical parameters, such as temperature and humidity, ensuring optimal conditions in the cold store. The system provides real-time data, allowing for immediate adjustments to maintain peak efficiency.
- Automated Control Adjustments: The system automates crucial processes, such as defrost cycles and compressor usage, minimising human error and ensuring smooth operation with minimal manual intervention.
- Sustainable Refrigerants: i-Air uses R290, a refrigerant with a low Global Warming Potential (GWP of 3), reducing the environmental impact of refrigeration.
- Minimal Refrigerant Charge: The system’s design requires a minimal refrigerant charge, reducing both the risk of leaks and the overall environmental impact.
The i-Air Solution at Dale Brothers:
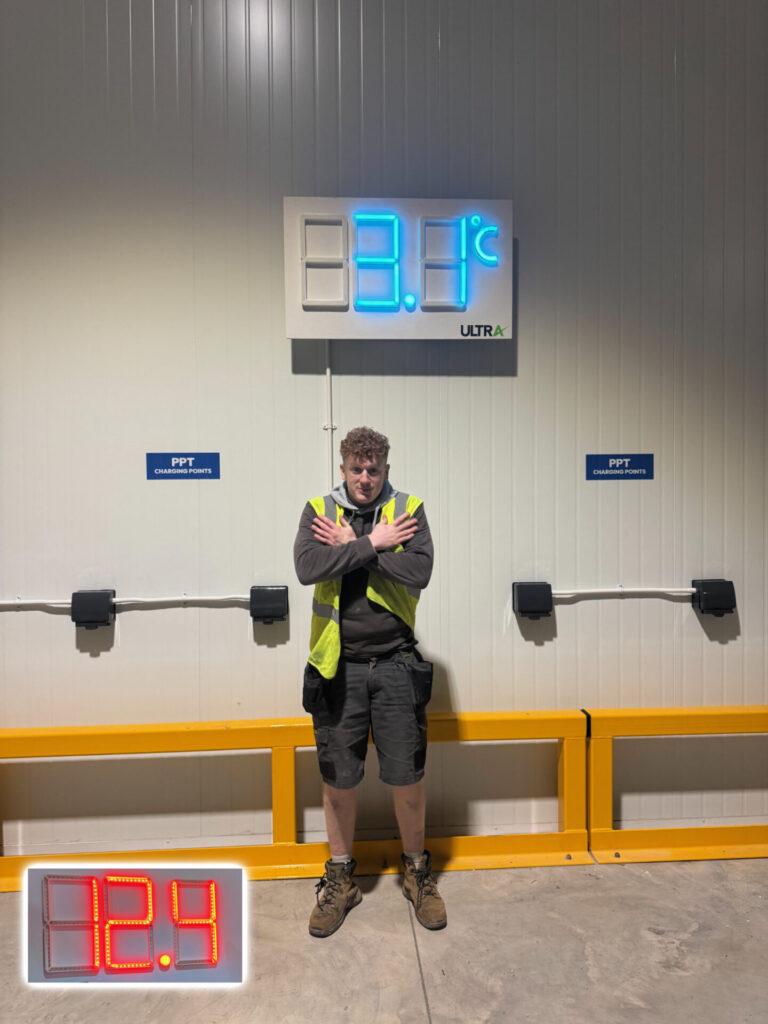
Dale Brothers’ first refrigerated warehouse posed a significant challenge: to deliver a reliable, efficient, and environmentally responsible cooling system for palletised chilled products. The coldstore, measuring 55 metres long, 20 metres wide, and 6 metres high, required a system capable of meeting the demanding cooling requirements while also delivering energy savings and minimising environmental impact.
The i-Air solution provides several key benefits for Dale Brothers:
- Custom Air Delivery System: the unique air delivery system ensures even temperature distribution throughout the coldstore meaning all palletised products remain within the required temperature range, reducing the risk of spoilage and product loss.
- Energy Savings with Rotational Shutdown: The i-Air system can automatically shut down one of its two refrigeration units during periods of low cooling demand. This rotational shutdown reduces energy consumption without compromising temperature stability, resulting in cost savings and more efficient operation.
Bespoke LED Temperature Display: A large, highly visible LED display was installed to provide staff with real-time temperature monitoring. The display changes colour to indicate temperature deviations, allowing for quick, intuitive responses to faults or issues in the cold store. This feature enhances monitoring efficiency and safeguards product quality.
Energy and Environmental Performance:
One of the most compelling aspects of the i-Air system is its energy efficiency and environmental benefits. Operational data are now being collected for comparison against design expectations, and early indications do not disappoint.
At the design stage an analysis was carried out comparing the i-Air system to traditional refrigeration systems using R407F, R449A, and CO2 refrigerants. The findings were remarkable:
- Annual Energy Savings: The i-Air system consumed just 45,783 kWh annually, compared to the reference system’s 51,965 kWh. This resulted in an 11.9% energy savings over the next-best conventional system.
- Lifecycle Cost Benefits: When factoring in energy and maintenance costs, i-Air demonstrated a significantly lower lifecycle cost compared to traditional refrigeration systems, with a payback time of around 4.5 years.
- Carbon Footprint: The i-Air system’s low refrigerant charge, combined with the use of low-GWP refrigerant R290, resulted in the lowest CO2 lifetime emissions among the systems compared, making it a highly sustainable solution for companies looking to minimise their environmental impact.
Customer Feedback:
Dale Brothers has expressed strong satisfaction with the i-Air system, particularly praising its:
- Energy Efficiency and Cost Savings: The system has delivered excellent energy efficiency, resulting in lower operational costs.
- Quiet Operation: The i-Air system operates with minimal noise, contributing to a quieter and more comfortable working environment for staff.
- Reliable Temperature Control: The stable and reliable cooling ensures that products are stored within optimal conditions, preserving quality and reducing spoilage.
- User-Friendly Interface: The intuitive control interface and remote monitoring capabilities have made it easier for staff to manage the system, enhancing operational efficiency.
Conclusion: A Bold Step Towards the Future of Cold Storage
The use of i-Air technology into Dale Brothers’ cold storage facility represents a significant step forward in the cold storage industry. By embracing cutting-edge technology and innovative design, the system has not only improved operational efficiency but also contributed to sustainability goals through energy savings and a reduced carbon footprint.
As the cold storage sector continues to evolve, i-Air offers a compelling solution for businesses seeking to meet the growing demands for energy efficiency, environmental responsibility, and operational flexibility. With its proven benefits, i-Air is set to become a key player in the future of cold storage refrigeration, demonstrating that innovation and sustainability can go hand in hand. For companies like Dale Brothers, embracing such innovation is not just about improving efficiency—it’s about leading the way to a more sustainable, efficient, and profitable future in the industry.
If you would like to discuss aspects of your existing refrigeration equipment, or want to talk about a new project, please get in touch by emailing us today at info@ultraref.co.uk or calling us on +44 (0) 330 2232404.