Cold stores and blast freezers are high-risk environments, and businesses have a legal duty to understand and manage these risks. Here Steve Shipp and Anthony Lomas of Ultra Refrigeration explore the nature of those risks, how they can be minimised and the part that can be played by good refrigeration system design.
General Health and Safety in cold stores*
In the UK, health and safety at work is governed by the Health and Safety at Work etc. Act 1974, which outlines an employer’s responsibility towards its employees, contractors and members of the public. The regulations, identified by the Health and Safety Executive (HSE), require businesses to apply specific and rigorous policies designed to recognise and minimise the risks that arise as a result of its operations.
This is important to prevent accidents that can lead to serious injuries, or worse, for both staff and visitors. If an accident happens, it can also have other consequences for a business, such as legal action, fines, business downtime (which means losing money), damaged equipment, and bad publicity.
By their very design, cold stores, blast freezers and other temperature-controlled areas may create working environments that are inherently hostile to human life due to low temperatures and the rapid movement of cold air. Additional risks may be created by (and not limited to): the increased chance of accidents such as slips and falls caused by condensation, freezing surfaces and ice; reduced mental faculty, dexterity and reactions of workers caused by lower temperatures; and the presence of moving equipment such as forklifts.
There are also potential risks associated with the refrigeration system itself which is often, but not always, located in a separate plant room outside the cooled space. A separate plant room allows employers to restrict access to the equipment to authorised personnel only, as there are heightened risks associated with electrical machinery.
The refrigerants used in these systems are often hazardous – toxic and/or flammable – and are governed by their own regulations, so require very specific risk assessments. Preventing and managing the risks associated with potential leaks of these refrigerants is an important responsibility for employers.
Safer by design
While the responsibility for Health and Safety compliance lies firmly with the employer, the role played by good refrigeration system design in keeping the workplace safe should not be overlooked. The fact that cold stores are becoming more ‘intelligent’, with automated storage systems which minimise manual handling of goods, cannot completely eliminate the need for humans to enter the refrigerated space; perhaps for inspection, for maintenance or to fix problems. The equipment located within this space should be designed to minimise the time required for human intervention.
“We recently attended a site where this aspect of safety clearly hadn’t been considered at the design stage,” says Anthony Lomas. “Our client asked us to replace the defrost heaters on the evaporator as they weren’t operating effectively. Unfortunately the evaporator had been installed so close to the side wall that the elements couldn’t be removed without dropping the evaporator. This apparently quick and simple task now turned into a major job requiring specialist access equipment and many more hours working at -20°C as the customer, understandably, didn’t want to turn off the cold store. All this could have been avoided; had we designed this cold store, as we have done in the past, we would have specified low pressure hot gas defrost, which effectively removes the need for heating elements altogether and can be more energy efficient if it can use free heat from elsewhere,” Anthony adds.
“Even better,” suggests Steve Shipp, “would be a design that removes all the equipment from inside the cold store and instead delivers ducted cold air into the space. This eliminates the need to enter the cold store for maintenance, and leaves more space in the store for produce. The Ultra iAir is just such a system,” says Steve.
Fail safe
When humans are required to enter the refrigerated space, safety guidelines should be followed to avoid lock-in, reduce lone-working, ensure training is provided on good working practices, provide adequate PPE and minimise the time spent in the cold.
Through good design at the outset, the cold store and refrigeration system can provide assistance if the unthinkable does happen; including emergency stop buttons, ‘trapped-man’ alarms, door safety mechanisms to enable personnel to get out from inside a ‘locked’ door, emergency lighting and emergency exits. These incorporated safety elements are not all created equally.
“Trapped-man buttons are mandatory on blast freezers,” says Anthony, “but it doesn’t always stop the refrigeration system or the fans working – it usually only raises an alarm so you hope someone comes to find you quickly. We design our blast freezers so the trapped-man button turns off the system and the fans – this immediately stops the rapid flow of cold air that is designed to remove heat fast, to give the operative more time to survive,” he says.
“And in terms of design,” says Steve, “there’s a safety aspect which maybe people don’t think about. When an emergency button is activated we design it so it’s not making a circuit but it’s breaking a circuit. This way we make sure it always fails safe; so if the switch fails, or a connecting wire breaks or indeed if the button is pressed, the circuit breaks and the alarm sounds,” he says.
Ensuring regular checks by design
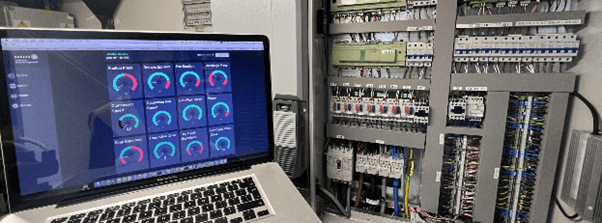
These safety systems must of course be regularly checked and tested to ensure correct operation. In addition, the refrigeration system itself should be monitored for safe and efficient operation; this can potentially reduce the need for intervention or maintenance and eliminate the need for humans to enter the cold space. This monitoring function can be incorporated into the initial design, as Anthony explains.
“There’s a feature on the customisable RDM controllers we use called Temperature Performance Indicator (TPI). This facility monitors the performance of a chosen indicator – this could be temperature, pressure or any other variable input. So, for example, if the temperature of the store should be 4°C and there’s a high temperature alarm set to go off at 8°C, but the room constantly runs at 7.5°C that’s not ideal; but similarly it’s not setting off the alarm either, so may go undetected for long periods. The TPI function monitors how far the variable is from its set-point and for how long, so a traffic-light system can be used to analyse system performance trends – this helps engineers diagnose certain problems that can be dealt with perhaps before maintenance is required. The TPI can be programmed to sound an alarm when a trend has been at a certain non-optimal level for a given time,” he adds.
A note on refrigerants
Many refrigerants are flammable, toxic or both, and the cold store and refrigeration system design should take into account any risks associated with the escape of these gases.
In the case of flammable refrigerants, the design needs to consider the point at which the concentration of the gas in air makes it flammable, because of the oxygen required to support the combustion. The size of cold store is relevant; even if all the refrigerant leaked into a large cold store it may not reach the flammability threshold but might potentially displace air to a dangerous level.
The system can incorporate a sensor that detects the gas, in parts per million (ppm), both upper and lower levels and automatically decide what to do with that information: e.g. sound an alarm, pump down the system or activate a mechanical extraction system.
*More information
For more information about Health & Safety in cold stores we recommend the following links…
- Health and Safety at Work etc Act 1974; https://www.legislation.gov.uk/ukpga/1974/37/contents
- Cold Chain Federation publication: KEEPING PEOPLE SAFE IN A COLD STORE: https://www.coldchainfederation.org.uk/publications/
If you would like to discuss aspects of your existing refrigeration equipment, or want to talk about a new project, please get in touch by emailing us today at info@ultraref.co.uk or calling us on +44 (0) 330 2232404.