In an industry under increasing regulatory pressure to innovate, Ultra Refrigeration has taken a bold step forward with the introduction of its new A2L-ready condensing unit range. But this launch isn’t just about a product—it’s about a philosophy. A way of thinking that places technical rigour, real-world application, and long-term sustainability at the heart of every decision.
Managing Director Steve Shipp outlines the challenges, insights, and thinking behind the process—from early concept through to real-world testing and production.
Why Now? Meeting a Market Need Before the Rules Demand It
The motivation to develop an A2L-compatible range wasn’t driven by current UK regulation—but by the direction of travel. We didn’t have to move to A2Ls yet but at Ultra we don’t wait to be told. We design ahead of the curve.
Our decision to act now—before legislation forces the market’s hand—reflects both strategic foresight and a desire to serve a growing segment of customers looking for future-ready systems. Some UK suppliers are still offering units operating on transitional A1 refrigerants, but that creates a ticking clock on viability. We wanted to offer something that will still make sense five or ten years from now.
Designing for Reality: What the Market Actually Needs
While our A2L condensing unit range might be new, our approach to product development isn’t. Innovation for us usually starts with the customer. We rarely create in a vacuum. It’s either a tweak to something we’ve done before, or it’s a completely bespoke system based on a specific need.
In this case, that need was twofold: future compliance and real-world efficiency. CO₂ and ammonia, while attractive in theory, present cost, complexity, and safety challenges in certain applications—especially in commercial kitchens, convenience stores, and smaller cold stores.
You’ve got to have deep pockets for CO₂. It’s not just the capital cost—it’s the energy, the training, the servicing. And ammonia’s simply not viable in smaller systems. A2L refrigerants like R-454A fill that middle ground.
Building the Range: A Scalable Design Philosophy
Rather than releasing a traditional step-by-step product range, we’ve focused on creating a scalable platform—a design framework adaptable to different applications and capacities. From blast freezers to cold store units, the same engineering principles underpin each build.
We’re not a high-volume producer offering off-the-shelf boxes. Each system is tailored for its application, but the underlying design—the separation of circuits, the resilience, the control logic—is consistent across the board.
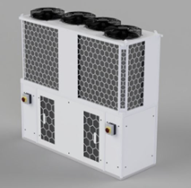
One standout innovation in the range is our Duty Standby design, featuring full N+1 redundancy, which duplicates all critical components—compressors, fans, evaporators, condensers—so that no single point of failure can bring the system down. Originally developed for critical applications like pharmaceutical storage and forensic evidence preservation, it’s now being deployed by clients like the British Antarctic Survey where reliability and redundancy are absolutely crucial.
Overcoming Challenges: From Components to Compliance
Developing for A2L refrigerants came with more than a few hurdles. Initially, the biggest challenge was component availability. It wasn’t that we needed components that were fundamentally different from existing ones—it’s that they hadn’t been tested and certified for A2L use. Without that approval, we couldn’t get them through PED compliance.
As part of the development journey, we also had to navigate new rules around the pressure equipment directives, including brazing standards and leak detection requirements. There’s no middle ground regarding the flammability issue – either the refrigerant is flammable or it isn’t, and the legislation treats it accordingly. It adds complexity to the design and manufacturing process, but it also drives higher standards.
Testing in the Real World
True to Ultra’s philosophy, the new A2L units weren’t signed off until they’d been properly tested in the field. One trial, in collaboration with Climalife, involved using R454A in a blast freezer to assess real-world behaviour and energy performance. All the simulations in the world can’t tell you how something will perform in reality – you’ve got to put it in a real plant, with real products, and see what happens.
One unexpected issue did emerge from the field trials. In early installs, some of the sensitive leak detectors were triggering nuisance alarms—not because of refrigerant leaks, but because of background hydrocarbons released by packaging materials or propane-fuelled trucks operating nearby. The solution was to recalibrate the sensors to trigger only above 80% of the lower flammability limit, rather than the default 20%.
Futureproof by Design
By building the A2L range to meet the more stringent safety and performance requirements of modern refrigerants, Ultra has created something even more valuable: flexibility. Our A2L units can still be charged and used with A1 refrigerants for now, but when those are no longer available for use, either by non-availability or through legislation, the system is already A2L compliant. It’s a futureproof design.
In many cases, the A2L refrigerants being used also outperform the transitional options. R454A gives around 7–8% more capacity than R-449A, so we’re not just swapping refrigerants—we’re offering more efficient systems, too.
More Than Compliance: The Bigger Picture
For Ultra, this project isn’t just about keeping up with regulation. It’s about doing refrigeration the right way.
A lot of legislation doesn’t benefit the end user. It just costs them more money. So our job is to make sure that if they’re going to spend more, they get a better outcome—more resilience, better energy efficiency, or lower total lifecycle cost.
This philosophy is also shaping how we advise clients. For example, we’ve recently had a high-end ice cream manufacturer torn between CO₂ and F-Gas systems for a new freezer room. We provided a lifecycle cost analysis of multiple refrigerant options, including a hybrid cascade system using CO₂ for the low stage and A2L for the high stage which the customer is now considering.
The goal is to make sure the customer understands the full picture—not just the initial price tag. Sometimes the cheapest system costs more in the long run.
A Voice for the Industry
We’re not just developing products; we’re also advocating for smarter F-Gas legislation. We would support a tiered framework, which would allow higher GWP refrigerants for niche, ultra-low temperature applications, rather than a blanket 150 GWP cap.
You can’t just say, ‘use CO₂ or ammonia everywhere.’ Every refrigerant has trade-offs. A one-size-fits-all rule punishes the people who are doing the most technically demanding work.
Conclusion: Built for Today, Ready for Tomorrow
Ultra’s new A2L condensing unit range is more than a product launch. It’s a statement of intent. A demonstration of what happens when engineering leads, rather than follows, regulation. When practical expertise, environmental responsibility and customer needs are all part of the same conversation. There are no silver bullets here. Every solution has compromises, but if you understand the trade-offs—and build systems that are honest about them—you’ll always be in a stronger position.
If you would like to discuss aspects of your existing refrigeration equipment, or want to talk about a new project, please get in touch by emailing us today at info@ultraref.co.uk or calling us on +44 (0) 330 2232404.