Ultra: A Victim of Our Own Success?
It’s the middle of summer. Temperatures are soaring, systems are under maximum load… and our phones are quiet.
At a time when breakdown calls would usually be climbing, we’re experiencing something unexpected — near silence. But it’s not due to lack of business. In fact, quite the opposite.
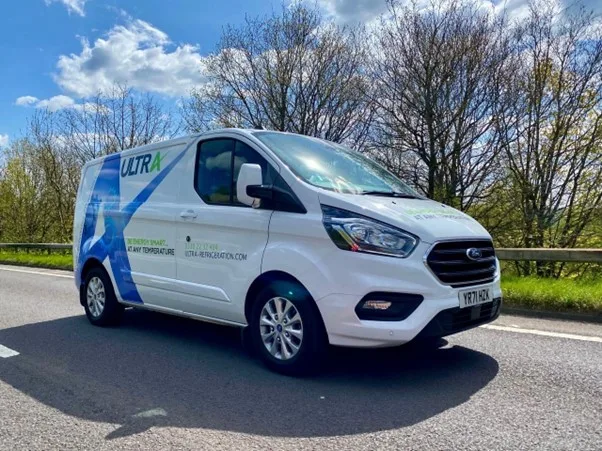
We’ve become a victim of our own success.
Thanks to the consistently high standard of routine maintenance and repair work carried out by the Ultra team, our customers are enjoying smooth, uninterrupted performance — even during one of the most demanding times of the year. Systems are holding steady, energy use is under control, and site managers are sleeping a little easier.
While we’re always ready to respond to urgent issues, it’s incredibly rewarding to see our proactive approach paying off — where preventative maintenance really does prevent problems.
And if you’re not already working with us, here’s our invitation:
“Join the growing list of customers who never need to call us.”
(Well… almost never.)
Join the growing number of businesses who no longer worry when the mercury rises — because they know Ultra has already taken care of the details. From tailored service plans to intelligent upgrades, we help you get ahead of issues, not chase after them.
Thrive in ’25: Sensors, Measurement, Cost Control
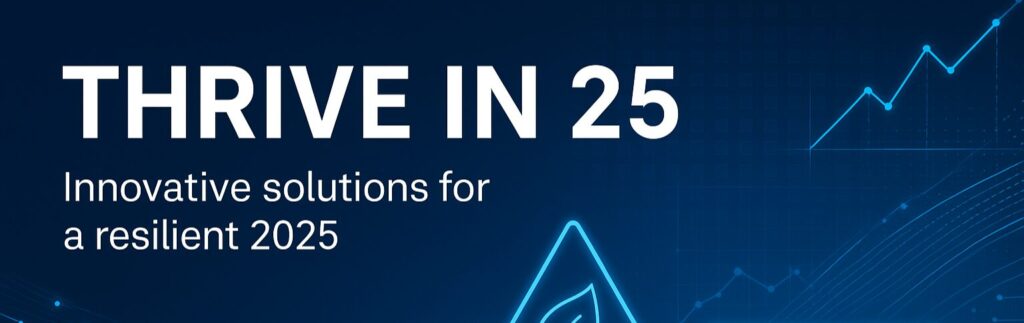
With energy prices staying stubbornly high and wider operational costs continuing to climb — from rising wage expectations to increased employer contributions — businesses are under increasing pressure to squeeze more from every resource. As summer sets in, refrigeration and cooling systems work harder to keep up, naturally driving up energy consumption and running costs. In this climate, boosting efficiency isn’t just good practice — it’s vital for keeping expenses in check and protecting long-term profitability.
This Month in Series 5: Practical Energy Solutions for Refrigeration
In this edition of our newsletter, we focus on the technologies that deliver immediate and measurable savings. At Ultra, we’re dedicated to supporting your business with proactive strategies to tackle today’s energy and cost challenges.
By adopting the latest innovations in intelligent refrigeration control and advanced energy management, you can drive down energy usage, cut maintenance costs, and boost your sustainability credentials.
Find out how Ultra’s bespoke solutions can help your business stay agile, competitive, and profitable in today’s demanding economy.
The Ultra Energy-Saving Technology Series
Building on the foundations we’ve laid in Series 1 to 4 of our energy-saving journey, we continue to showcase the advanced refrigeration technologies available from Ultra.
In Series 1, we explored Electronic Expansion Valves (EEVs), in Series 2, we highlighted the advantages of EC condenser fan motors and series 3 covered speed controlled compressors.
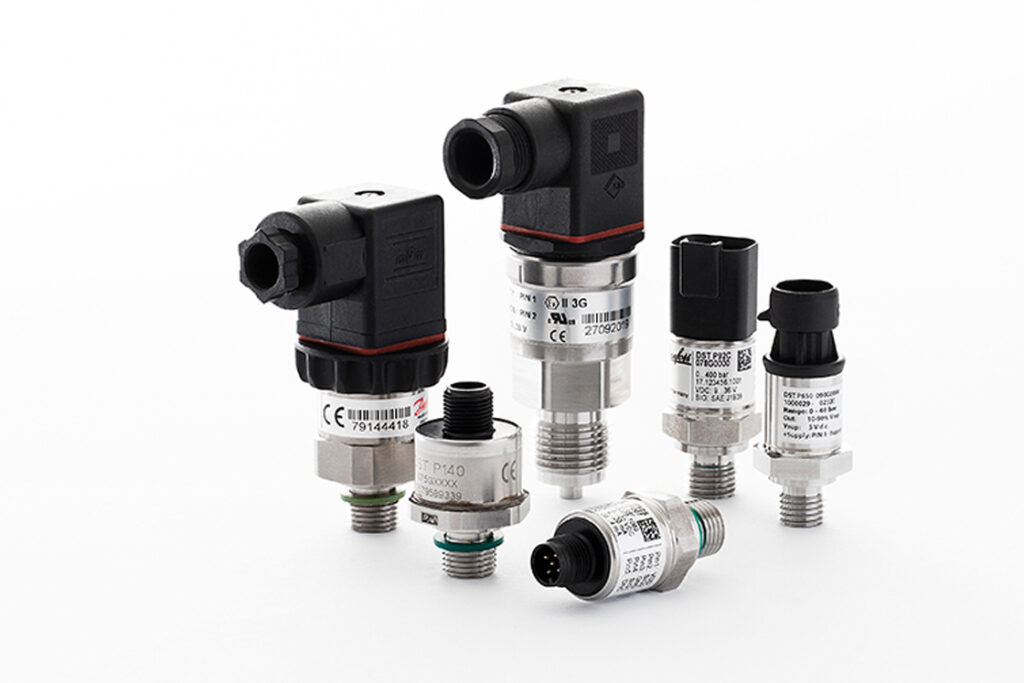
To unlock the advantages of these technologies, an advanced control system is essential, which we covered in series 4. But even the most advanced control systems are only as good as the data they receive, That’s why in Series 5, we’re focusing on the unsung heroes of refrigeration control: sensors. From simple switches to sophisticated transducers, these components provide the real-time data that enables smart systems to make intelligent decisions.
Series 5: Sensing the Difference
Real-Time Data for Smarter, Safer, More Efficient Systems
✔ Precision Monitoring = Better Decision-Making
✔ Early Detection = Faster Response and Less Downtime
✔ Data Transparency = Informed Maintenance and Optimisation
![]() These are the foundation of any refrigeration system — measuring air, pipe, and product temperatures to ensure accurate control. Precision here means tighter temperature bands, less cycling, and improved product safety. With modern controllers and distributed I/O, it’s now possible to add far more temperature monitoring points than before — enabling deeper insight and more granular control across complex systems. |
![]() Think of these as a set of digital gauges permanently connected to the system. Just as an engineer might arrive on-site and attach gauges to check suction and discharge pressures, transducers give us that same visibility — but continuously, 24 hours a day. This real-time data allows the control system to respond dynamically to changing conditions, balance performance, protect compressors, and flag potential faults before they become failures. |
![]() Used to track energy consumption in real time, power meters help identify inefficiencies, verify savings, and optimise system loading — all critical in today’s energy-conscious climate. Waiting until the bill comes in is already too late – this live information gives us the opportunity to identify inefficiencies before months of over-spending. |
![]() When monitoring glycol or secondary refrigerant circulation, flow meters help verify system health, detect blockages, and ensure heat exchangers are performing as expected. |
![]() Monitoring airflow across evaporator fans ensures they are operating correctly and allows the system to constantly adjust fan speed to maintain optimal airflow. These sensors also play a key role in defrost strategy — helping to determine the right time to initiate defrost cycles based on actual conditions, rather than relying solely on fixed timers. The result is improved efficiency and reduced unnecessary energy use. |
![]() These sensors provide critical safety monitoring, helping detect refrigerant leaks early. This not only prevents product loss but also reduces environmental impact and ensures compliance with F-Gas regulations. |
![]() Simple but essential. Door switches detect open doors on coldrooms, reducing unnecessary energy loss. Enable the option to turn off the system when the door is open, bring on the lights and alarm if the door has been left open. Meanwhile monitoring the essential safety switches ensures protection in emergency conditions and gives clear, immediate guidance to the source of any fault. |
Together, these sensors create a live picture of system status — allowing control systems to make informed adjustments in real time. And this is just the beginning. With the ability to integrate virtually any device using standard outputs or protocols, we can tailor monitoring and control to suit each site’s specific needs.
Spotlight
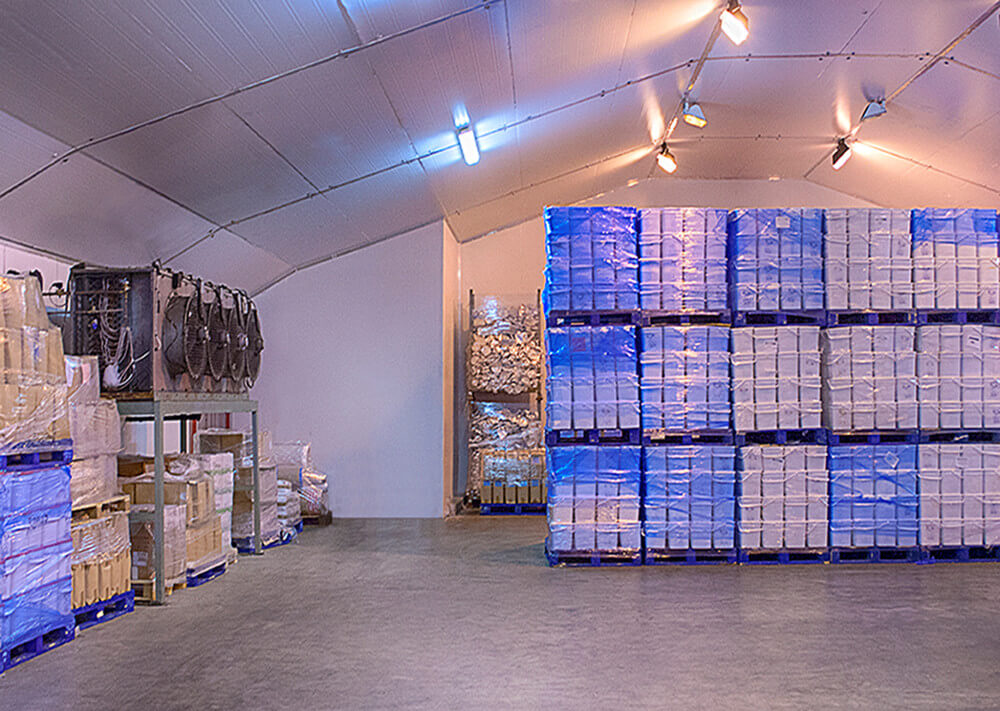
Intelligent Retrofit & Energy Monitoring at Haskell & Co
Haskell & Co, a cold storage and blast freezing facility in Nottinghamshire, partnered with Ultra to modernise their legacy plant controls without disrupting operations. While their mechanical systems were sound, outdated panels left them with no remote access, limited diagnostics, and rising energy costs.
Ultra delivered a phased retrofit using RDM hardware and custom software, starting with condenser and compressor control upgrades. Key improvements included pressure-based fan control, automated compressor rotation, and the removal of unreliable mechanical switches.
Remote access and real-time monitoring were introduced via an RDM data manager, and energy monitoring is now being added—enabling true cost-per-cycle analysis and early fault detection through kWh tracking.
The result? Improved system stability, reduced manual intervention, and greater visibility. With the next phases already underway, Haskells is on track for a fully intelligent, energy-aware plant.
Want to Learn More?
Whether you’re upgrading existing systems or planning a new installation, our team is here to help you explore how Ultra Heat Recovery can benefit your operation.