Electric Vehicle (EV) Battery Testing, Research & Development
CLIENT: | MAHLE Powertrain |
PRODUCT: | CO2 Refrigeration Systems and Air-Handlers |
TEMPERATURE STABILITY: | ±0.2 degrees celsius |
Background
MAHLE Powertrain, an international engineering partner to the automotive industry, provides research, development and testing services to a wide range of vehicle manufacturers. MAHLE Powertrain has developed capabilities and techniques to support the development of EV technologies as well as building a new facility for the assembly and testing of battery modules and full-size battery packs.
MAHLE Powertrain approached Ultra to design, build and install three climate-controlled battery test chambers within their new facility in Northampton, UK.
Client’s Requirements
Temperature Range
To achieve a temperature range of -40 to + 60°C and be able to maintain a setpoint anywhere in between.
Temperature Precision
To deliver exceptional temperature precision of better than 0.2°C, ensuring accurate and reliable test conditions.
Temperature Performance
Capable of increasing or decreasing temperature by 100°C within 30 minutes to provide rapid shock-test capabilities.
Control software
Required to interface with the client’s control system to synchronise control changes with other processes during testing.
Longevity
Must utilise a low GWP refrigerant which will be available during and after the phase-down of F-Gas refrigerants.
Integrity
Insulation must be suitable for temperatures of -40°C and must be pressure-tight to prevent ingress of external ambient air during use.
Testing Environment
The system had to allow for the charging and discharge of the EV batteries whilst under test.
Ultra’s Solution
Ultra engineered and delivered three state-of-the-art temperature-controlled test chambers, including the refrigeration cooling plant, heating matrix, controls and associated interfaces with the existing services and Building Management Systems (BMS). In order to meet the client’s exacting requirements, pushing the boundaries of precision and performance, the design solution incorporated the following features.
CO2 refrigerant
CO2 refrigerant was chosen as the most appropriate low GWP solution, with a high degree of confidence regarding its long-term availability and serviceability.
Given the required temperature range down to -40°C, there was a potential issue with the CO2 triple point. This was overcome through careful pressure management, via strategically placed sensory inputs and the bespoke control software, which also featured a raft of safety measures.
To overcome CO2’s inefficiencies at critical point (around 22°C ambient) we linked into the client’s existing on-site supply of chilled water at 5°C. With some careful control and monitoring of the chilled water temperature and flow, we were able to avoid any super-critical operation and maximise system efficiency.
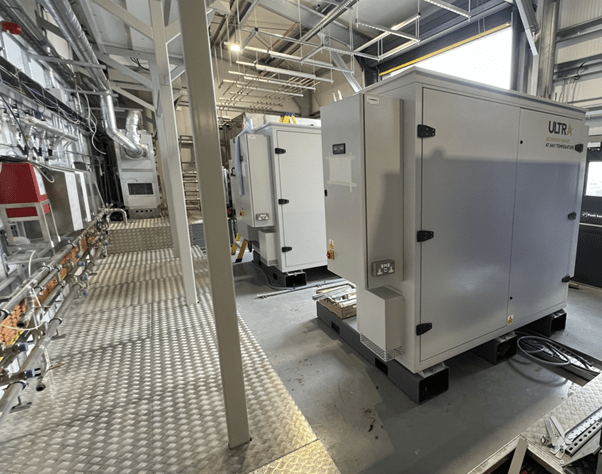
MAHLE Powertrain refrigeration installation
Refrigeration plant
Each chamber features a fully enclosed housing with four Bitzer reciprocating compressors operating in pairs at different temperature ranges, or all together as an externally compounded boost system to achieve -40°C with inter-stage cooling.
The compressors were individually speed controlled via the LUA block software (a feature of the chosen RDM controllers), with specially written new code, which ensured the required +/-0.2°C temperature accuracy.
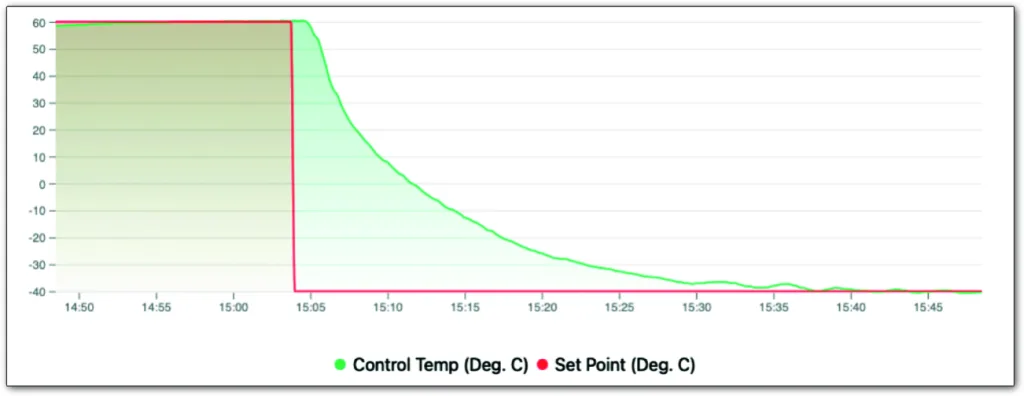
MAHLE Powertrain Temperature/Time Graph
Heating
The heating was supplied via an electric heater bank, mounted close to the evaporator. The elements were controlled using the PWM outputs from the RDM controller which enables the heaters to be pulsed on and off rapidly to achieve near stepless control.
No defrost system was required as the systems use dehumidified air.
In order to accurately control temperature at low load conditions (a level close to the compressors’ minimum speed capability), we opted to run the compressors at a speed they could comfortably maintain and then add heat using the heating elements, effectively ‘feathering’ the heating and cooling using the controls to maintain temperature accuracy.
In order to maintain accuracy of the actual air flow around the chamber, volumetric fan controls were used to automatically adjust the AHU fan to overcome the air resistance of differently shaped objects that might be placed in the test cell.
Web-enabled controllers
The systems were equipped with RDM’s TDB range of controllers. TDB stands for The Data Builder; in essence a blank controller which can be highly customised for specific applications where ‘non-standard’ or enhanced parameters need to be controlled. This enables custom software to be written, improving the reliability and efficiency of the control processes and to achieve functions that would otherwise be impossible with standard off-the-shelf controllers.
The controllers also feature a web-enabled user-friendly interface, remote connectivity and BACnet integration with the client’s master control system.
The BACnet was particularly important in this application as it enabled the test chambers to communicate with the client’s system to control the supply of air from their central dehumidifier, bringing dry air at 25°C into the chambers. By purging and demanding air at a known temperature we were able to speed the transition through the temperature range, both up and down, minimising the provision of heating or cooling.
Our highly tailored control software, using both logic blocks and the LUA programming language, played a pivotal role in managing the complex controls of the cooling systems, ensuring seamless operation and precise temperature control.
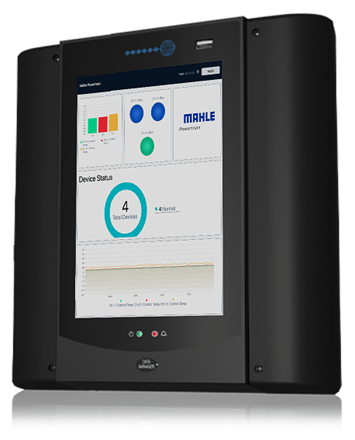
MAHLE Powertrain data manager
CAD design collaboration
Given the tight spaces involved within the existing building, and the need to link the test chambers and plant to chilled water pipework, humidified air ductwork and control systems, CAD models of the complete building were supplied by the client to inform our design and installation. This ensured a precision fit and a stress-free installation.
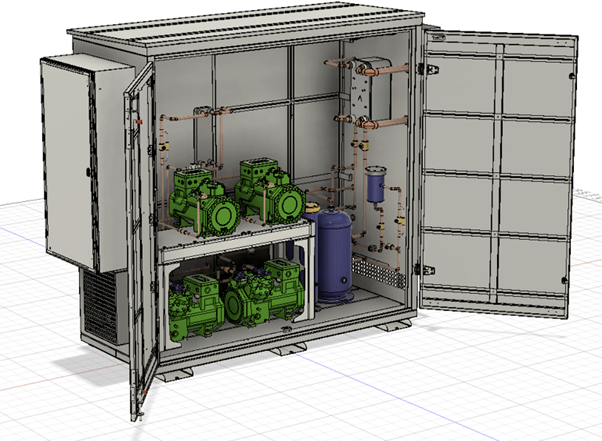
MAHLE Powertrain refrigeration schematic
Specially designed & 3D printed pressure relief valve (PRV) sensor
Given that these test chambers are not under continuous use or monitoring, unlike supermarket refrigeration for example, there is the possibility that the CO2 refrigerant could be evacuated from the system without the client being aware if a high pressure condition is present. To avoid this possibility, we designed a sensor to monitor the pressure relief safety valves to alert the client to such an occurrence.
Construction
The air handlers, designed to be air-tight yet serviceable, are constructed from polyurethane sandwich panels boasting both rigidity and good insulation. Featuring removable panels to access the evaporator and heater bank.
Dealing with pressure changes when air expands/contracts
Given the operating temperature range within the sealed chambers, we needed to devise ways of dealing with the internal pressure changes. For high pressures, release valves were installed. For low pressures, we needed to carefully control the intake of air from the on-site dehumidifier system by communicating the required demand via the software interface.
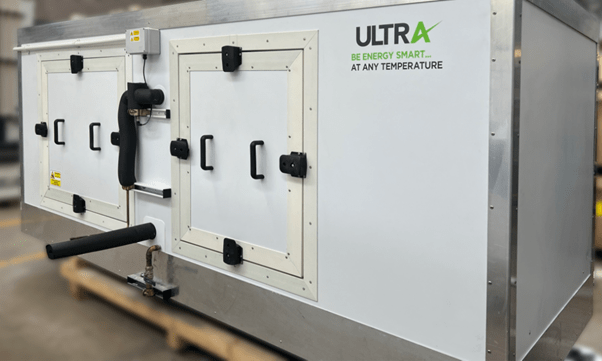
MAHLE Powertrain AHU
Conclusion
This case study showcases Ultra’s capability to design, build and install innovative and sustainable solutions that meet the evolving needs of industry whilst demonstrating our commitment to pushing the boundaries of technology.
The systems not only met but exceeded the client’s requirements, providing a robust and flexible platform for EV battery testing. The success of the project underpins Ultra’s position as a leader in the field of specialised cooling solutions for advanced testing applications.
If you would like to discuss a project requiring precision temperature control, please get in touch by emailing us today at info@ultraref.co.uk or calling us on +44 (0) 330 2232404.