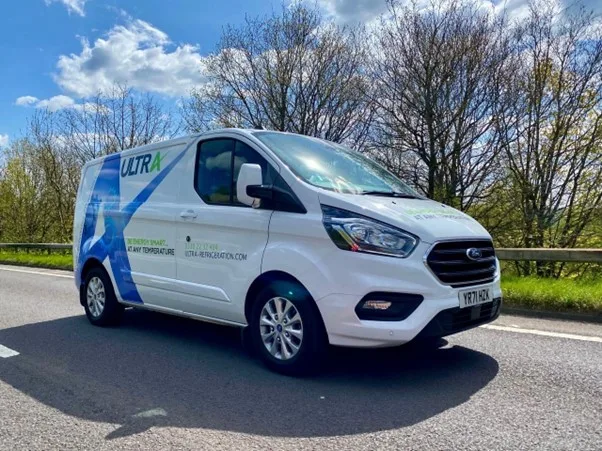
Ultra Refrigeration’s Steve Shipp and Anthony Lomas explain the importance of regular, planned, preventative maintenance and look at the benefits it brings to end-users and operators of commercial refrigeration systems.
Benefits of preventative maintenance
For owners and operators of commercial refrigeration systems, which may have an expected operational lifetime well in excess of twenty years, the benefits of regular, planned, preventative maintenance may seem obvious, but are certainly worth reiterating for clarity.
- Increased Efficiency: Regular maintenance will enhance the efficiency of commercial refrigeration systems, leading to lower running costs.
- Energy Savings: Well-maintained systems consume less energy, contributing to environmental sustainability.
- Quieter operation: Properly running systems make less noise and run for shorter periods.
- Prolonged Lifespan: Preventative maintenance can extend the lifespan of equipment, reducing the need for frequent replacements and lowering the lifetime costs of a system.
- Fewer breakdowns: A well-maintained system will suffer fewer breakdowns, particularly during critical periods.
- Increased profit: Minimising downtime and keeping food in optimum condition will boost product sales, reduce waste and stock losses.
- Peace of mind: Given the above benefits, end-users are safe in the knowledge that they’re not leaving the operation of their equipment to chance.
Best practice and tips for ongoing maintenance
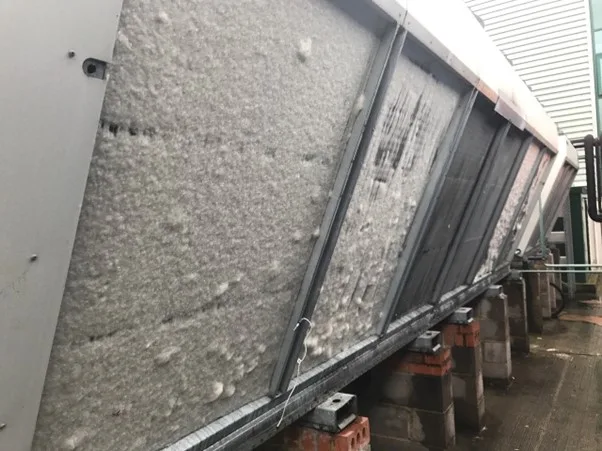
A condenser which is just 50% blocked will typically use 43% more energy.
For food retail and food chain businesses, the refrigeration system is of vital importance to the success of the operation. We would therefore expect operators to take the best possible care of their equipment on a daily and weekly basis, between scheduled maintenance visits. This would mean routine visual checks of system components, keeping condensers clean, regular product temperature measurements and any other available diagnostic monitoring. In fact, anything that could give an early warning of any potential problems or changes in the way the system is operating.
These simple checks, carried out in-house by operators with no formal refrigeration knowledge, can be a signal that it’s time to call in the experts.
If the business has access to a maintenance package with a trusted partner, then a call to the 24-hour help desk might be all that’s required to sort a problem. If not, an engineer could be requested to visit.
Many maintenance packages allow for preferential service rates, unlimited call-outs and on-site labour included in the fixed monthly charge, which can provide for peace of mind.
Also included in any package should be two routine maintenance visits per year by a fully qualified refrigeration engineer. If there are no other callouts or problems, this is when the system receives a full maintenance check-up to identify any operational problems which can be put right during the visit or a subsequent service call.
We would always look at any diagnostic data that is available; this can be the key to identifying inefficiencies or the early signs of problems developing. The more data that’s available, the better, and historic data can be used to track trends in performance. The data may reveal a system that is operating slightly below its optimal performance level but is not sufficiently adrift to signal an alarm.
It’s important to correct this, not only for energy efficiency considerations, but also because, while a suboptimal system might function adequately most of the time, it holds the risk of catastrophic failure during peak demand, such as on the hottest day of the year when it needs to operate at maximum capacity.
We would always recommend that systems are built with as many data monitoring points as possible as the data will be invaluable in running the system efficiently. The up-front costs may be higher, but there will be numerous years of more efficient operation which will pay for the additional costs many times over. The RDM controllers we build into new systems have facilities for adding in monitoring points for data gathering, and these can sometimes also be retro-fitted to existing systems.
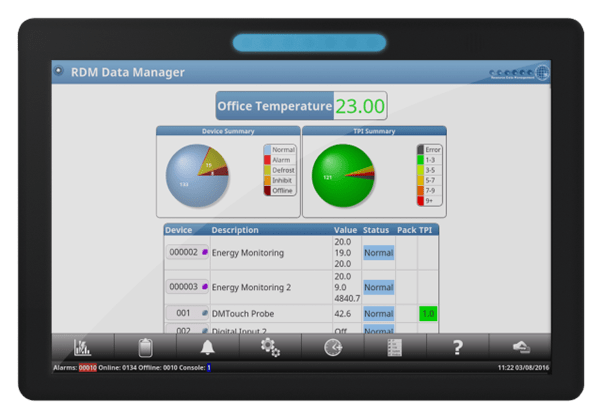
The RDM Temperature Performance Indicators (TPI) function is a sophisticated analytics tool designed for refrigeration systems that monitors temperature data to assess system efficiency. It uses historical and real-time data to calculate the optimal performance, flagging deviations and inefficiencies, and assisting in predictive maintenance to prevent potential system failures.
There is some seasonal rationale for preventative maintenance. It does make sense to ensure that a commercial refrigeration system is in tip-top condition immediately before entering the summer period when it is likely to be under maximum load conditions. Efficient operation will reduce the potential for breakdown during this period and, of course, reduce operating costs.
This also helps avoid another potential problem; because breakdowns are naturally more common during the summer, refrigeration engineers tend to be very busy fixing other people’s problems so might not be available to sort out your issue as soon as you would like.
More than a maintenance partner
Here at Ultra we try to be more than just expert, ‘hands-on’, fixers of commercial refrigeration systems for our clients.
We realise that not all of our clients are refrigeration experts; after all, they have a business to run so can’t possibly be expected to keep up with the latest technical and legislative changes affecting their fridge system.
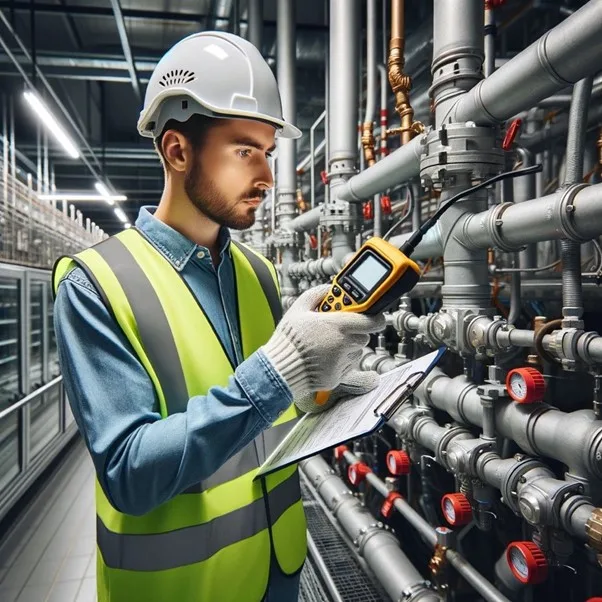
A more informal part of our ‘maintenance service’ is to advise our clients on these matters. This informal advice can take many forms. We aim to keep our clients ahead of their legal obligations in terms of F-Gas leak checks and perhaps any issues of food safety and hygiene in relation to their fridge system. Where appropriate, we’ll have conversations about operational aspects of good cold-store management such as: keeping doors closed; minimising personnel movements; general housekeeping; defrost regimes; cleanliness etc. In the background, as part of our own records (but frequently useful for clients as well!), we keep a detailed asset register of clients’ equipment and F-Gas records.
We also help our clients anticipate the future impact of legislative changes on their systems. For example, how the new F-Gas Regulations, which accelerates the reduction in HFC quotas, affect our clients’ systems, particularly those operating on R404a. Despite plans for a full phase-out of F-Gases, including newer, lower GWP alternatives like R449A, not being scheduled until after 2030, the suggested hastening of this phase-out, along with any potential supply problems in the interim, could affect equipment expected to function significantly longer than this timeframe – with some refrigerants already targeted for phase out as early as January 2025.
We can help clients talk through these issues and start to plan for any refrigerant and equipment changes.
Maintaining your business
The benefits of regular, planned, preventative maintenance by experts in refrigeration technology cannot be overstated. Here at Ultra, we ensure all our onsite engineers are fully trained, experienced and knowledgeable in all aspects of refrigeration technology. Through our training programme, including our apprenticeships, all our staff have well-rounded, hands-on refrigeration experience, including independent F-Gas certification and refrigerant handling expertise.
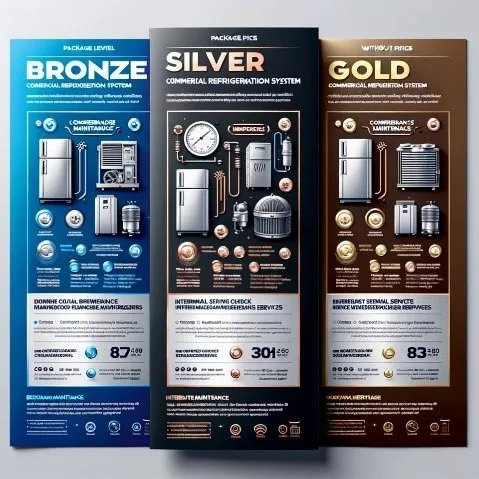
As your maintenance partner, we aim to offer you peace of mind for your business, not just your refrigeration system.
If you would like to discuss aspects of your existing refrigeration equipment, or want to talk about a new project, please get in touch by emailing us today at info@ultraref.co.uk or calling us on +44 (0) 330 2232404.