Dean Carpenter, Regional Refrigeration Supervisor at Ultra Refrigeration, shares his thoughts about his role as an experienced refrigeration service engineer.
A Day in the Life – Refrigeration Service Engineer
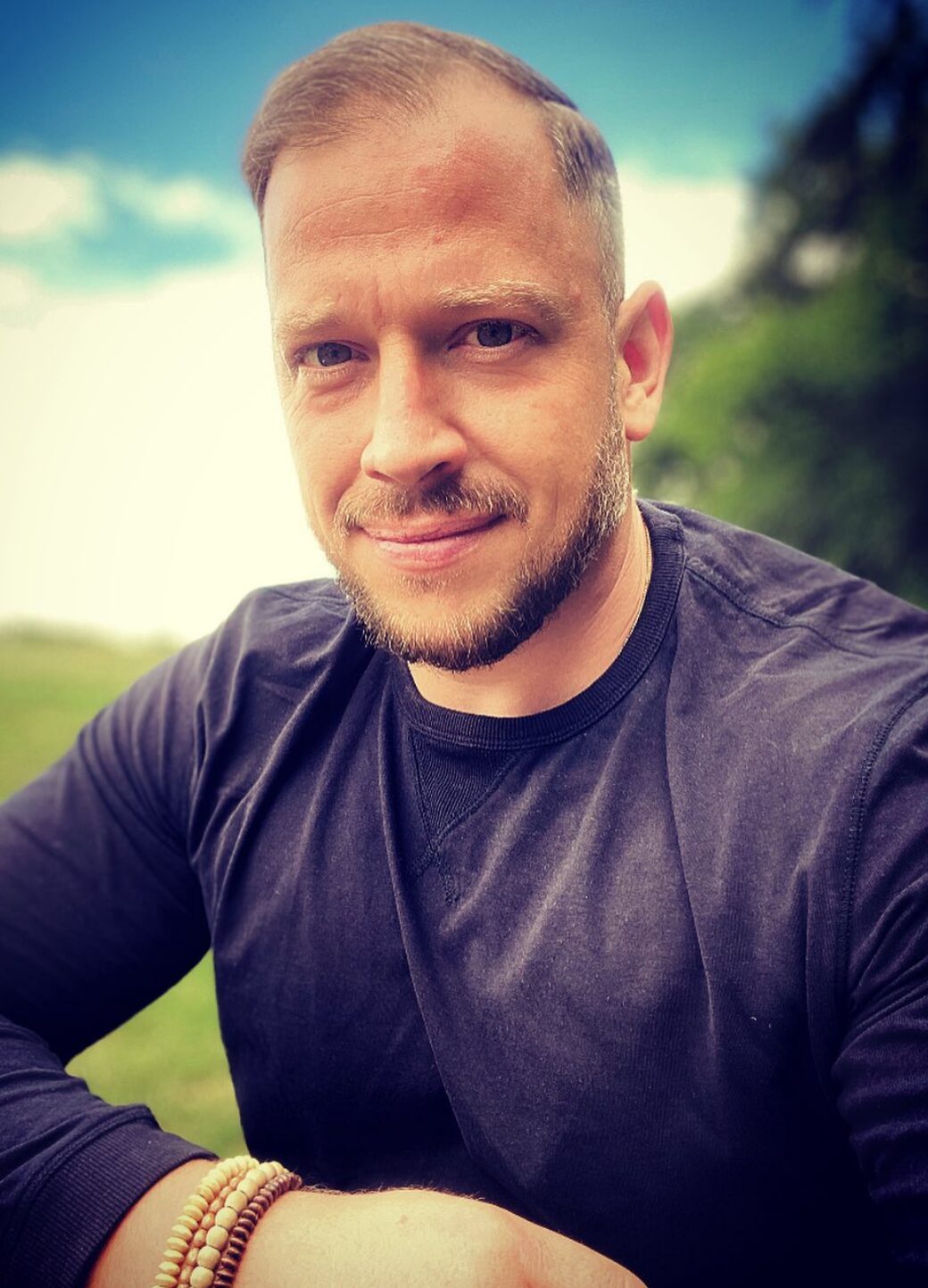
My morning routine generally starts around 5.30AM. Waking early allows me to get a head start on the day and ensure everything is in order. The first thing I do is check my overnight emails from the on-call engineer to confirm that my schedule remains unchanged and there are no emergencies. It’s crucial to stay on top of any last-minute changes to avoid unexpected surprises.
Next, I double-check my assigned jobs for the day. This involves reviewing the specific tasks, the locations of the sites I’ll be visiting, and the details of any parts that have been confirmed on-site by the office. This ensures that I have all the necessary equipment and materials for each job, minimising the risk of delays once I’m on the road. Planning the job order and route with the highest priority tasks first is essential for maximising efficiency and ensuring that urgent issues are addressed promptly.
Once I’m satisfied with my preparation, I gather my tools and equipment, making sure everything is in good working condition. This includes checking my van’s stock to ensure I have commonly needed parts and supplies. Being well-prepared can make a significant difference in how smoothly the day goes, allowing me to focus on solving problems rather than dealing with logistical issues.
Typical Service Call: Diagnosing and Fixing Issues Efficiently
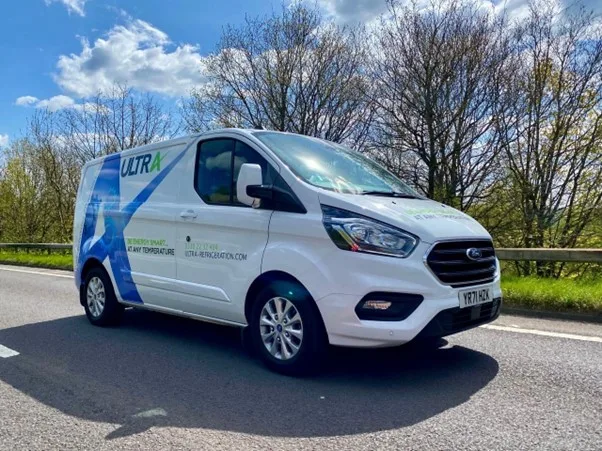
A typical service call might involve attending a site with a chiller case in a supermarket that has no airflow. On receiving such a call, the first step is to dial in remotely using RDM’s data management software to see if I can diagnose the issue before arriving on site. This remote access is a huge advantage as it allows me to understand the problem beforehand, saving time and increasing productivity. For instance, in this scenario, I might find that the air probes are reading incorrectly, which could indicate either a faulty probe or tripped evaporator fans.
Armed with this preliminary information, I head to the site, grabbing a replacement fan and the correct manufacturer’s probe from my van stock. On arrival, I’ll greet the staff with a smile and quickly check to see if my remote diagnosis was accurate. If the evaporator fans have tripped, I carry out electrical tests to identify the faulty fan, replace it, and switch the system back on. Watching the chiller case come down to the set temperature is always a satisfying moment.
After resolving the issue, I brief the client on my findings and discuss any concerns or other potential issues they might be experiencing. This is an important part of building trust and ensuring they feel confident in the service provided. While talking, I usually check the management system for any other alarms that might need attention.
Finally, I ensure the work area is clean, removing any signage or barriers, and do a quick sweep-up to leave the site as I found it. I also like to walk around the site to observe the equipment and cabinet furniture, checking for any signs of wear and tear that might need addressing in the future. Then, it’s back to the van to fill out the job report and send it to the office, wrapping up the call efficiently.
Maintenance: Preventing Future Breakdowns
Maintenance, though often seen as the less exciting part of the job, is crucial. Preventative maintenance is what keeps the phone from ringing at 2.00AM with urgent breakdowns and keeps customers happy by minimising unexpected disruptions. Regular maintenance tasks include cleaning condensers to prevent dust and grime build up, which can cause expensive component failures like compressors and fans, as well as high-pressure trips during warmer months.
Case cleans are another essential maintenance task. They help prevent water leaks and drainage blockages, which can be highly inconvenient for customers and pose health and safety risks. Regularly scheduled maintenance not only extends the lifespan of the equipment but also ensures it operates at peak efficiency, saving customers money on energy bills and reducing the likelihood of costly emergency repairs.
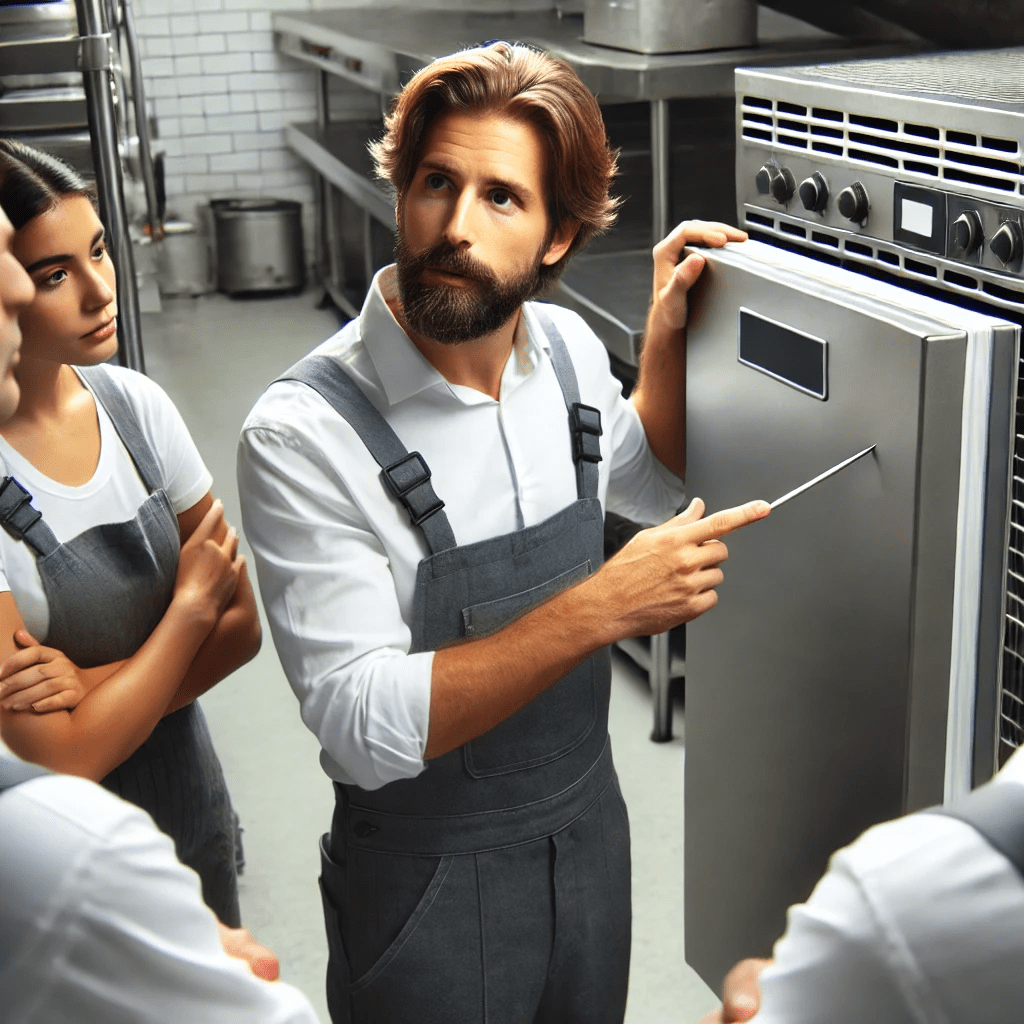
Emergency Repairs: Staying Calm Under Pressure
Emergency repairs are a critical part of the job that requires a calm, clear head. These situations can be stressful, but treating them like any other repair helps manage the pressure. Years of experience have taught me that panicking leads to mistakes and clouds judgment. Maintaining composure ensures that issues are resolved quickly and efficiently, meeting customer expectations and maintaining Ultra’s reputation for reliability.
For instance, if a customer’s cold storage room fails and there are tens of thousands of pounds worth of produce at risk, the pressure to resolve the issue swiftly is immense. In these high-stake situations, having a methodical approach is key. I assess the problem systematically, using both my technical knowledge and experience to find the quickest and most effective solution. This mindset helps me remain focused and effective, even under significant pressure.
The Refrigeration Systems: Diversity is key
One of the aspects I appreciate most about working at Ultra is the variety of systems we look after. Unlike engineers who work exclusively on specific supermarket chains, we encounter a wide range of refrigeration systems. This diversity includes everything from small commercial under-counter chillers to large distribution centre cold rooms, supermarket packs, water chillers, air handlers, heat recovery systems, and of course our own manufactured blast freezers and cold stores.
This variety enhances our knowledge and experience, setting us apart from competitors who might specialise in a specific type of equipment. Each type of system presents unique challenges and learning opportunities, keeping the job interesting and ensuring that we continuously develop our skills. For example, the technical complexities of a giant distribution centre coldroom are vastly different from those of a small commercial chiller, requiring a broad understanding of various refrigeration technologies and techniques.
Career Path and Experience: A Journey of Continuous Learning
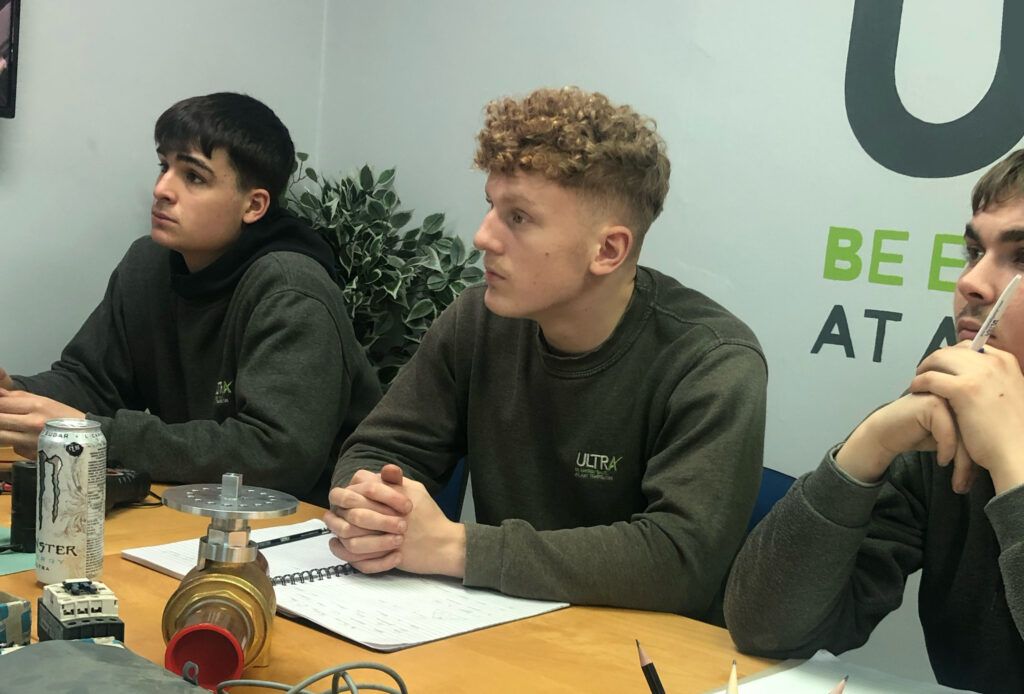
I’ve been at Ultra for ten years, following many years at my father’s refrigeration company. My role at Ultra involves not only service, maintenance, and breakdowns but also some installation work. This variety provides plenty of on-the-job training and real-life problem-solving which has been instrumental in growing my expertise and confidence.
Much of what I’ve learned has come from hands-on experience. While classroom training is essential for learning basic skills and industry specifics, such as refrigerant handling, real knowledge comes from tackling a wide variety of problems in real-life situations.
There is currently a significant shortage of skilled refrigeration engineers, and Ultra is committed to addressing the problem by investing in training for the new generation of engineers.
Skills and Qualities: Technical and Soft Skills
Refrigeration engineers need to be multi-disciplined, with skills in controls, electricals and plumbing as well as understanding the physics and chemistry behind refrigeration. Accurate diagnostics and a logical approach to fault-finding are essential. The clues to solving problems can often be found in the control software, and in many cases, this can be accessed remotely before we even get to the site. This remote access allows us to diagnose issues accurately and come prepared with the necessary parts and tools.
Soft skills are also crucial. As the face of Ultra, it’s important to build positive relationships with our clients; our role extends beyond technical repairs to include training and support.
At breakdown visits, we might face our customers when they’re under stress and we need to provide reassurance and efficient solutions. On regular service and maintenance calls, we have the opportunity to discuss equipment and industry trends in more detail. Customers appreciate our experienced view on any recommended enhancements to their equipment or methods of working, as well as any forthcoming legislation that might affect them in the future.
Conclusion: Every Day is a Learning Day
In the refrigeration industry, there’s a shortage of skilled engineers, making continuous learning and adaptation essential. Each day presents new challenges and opportunities for growth, reinforcing the importance of being prepared, knowledgeable, and customer-focused in every aspect of the job.
Every day is a learning day in this field. The variety of equipment, the range of problems encountered, and the different customer interactions ensure that no two days are the same. This constant learning and adaptation make the job rewarding and fulfilling. Staying current with industry advancements and continuously improving my skills ensures that I provide the best possible service to our customers, maintaining Ultra’s reputation for excellence.
If you are interested in a career in refrigeration, or would like to talk to us about your refrigeration equipment, please get in touch by emailing us today at info@ultraref.co.uk or calling us on +44 (0) 330 2232404.