Advanced system management for refrigeration systems is becoming a standard requirement for new designs and, increasingly, specified as a retro-fit to existing systems. These systems vary in complexity and the benefits they bring operators as Anthony Lomas, Operations Director of Ultra Refrigeration, explains.
Refrigeration System Management Timeline
This timeline highlights key developments in refrigeration system management over the decades, showcasing how technology has evolved to improve efficiency, monitoring, and control.
Evolution since the 1980s
The capability of refrigeration management systems has come a long way over the last 40 to 50 years. The 1980s saw the introduction of basic hard-wired alarm panels with limited functionality; these would provide a local alert when a system parameter exceeded its tolerance, but it would require an engineer to be called to physically examine the system to find out what happened, and why.
The 1990s saw the birth of end-to-end connectivity with cabinet and cold room controllers being connected to the monitoring system. This enabled localised control of set points, defrost and lighting control. Alarm dial-out was via the building’s intruder alarm and still required physical attendance to diagnose faults.
The early 2000’s brought modem connectivity which enabled some remote monitoring capability. Technology further improved from the mid-2000’s with the growth of the internet and faster connection speeds enabling significant advancements in the breadth of remote monitoring and the depth of information that could be conveyed.
Today’s advanced systems enable automatic real-time management of not only the refrigeration plant but also, if required, full integration with HVAC and lighting systems via the Building Management System (BMS).
These days we’re only limited by our imagination.
Monitoring v Management
The key change over the period has been the progression from simple, passive monitoring systems (local or remote alarms and perhaps some data collection) to advanced proactive management systems with detailed data collection and analysis.
This brings the ability to automate real-time adjustments to the operation of the refrigeration plant to minimise energy use, using feedback from multiple sensors measuring a range of operational parameters.
The feedback must compare the current performance of the system against the predicted ‘model’ performance at given conditions. This modelling of the ideal system performance, usually based on ambient temperature, is critical to get right from the outset as all automated management controls will aim to guide the system towards this ideal state. Management controls can now include custom software program modules to add functionality that fine tunes system performance for improved energy usage.
Benefits of advanced system management
1. Improved Energy Efficiency and Performance
Advanced system management provides real-time data about the condition and performance of refrigeration units, allowing inefficiencies and problems to be identified before they become serious. For example, out-of-pattern temperature fluctuations or system pressures, can quickly determine when a system isn’t operating at optimal levels. With this timely data, immediate corrective action can be taken, minimising energy wastage and improving overall system efficiency.
This not only helps lower operational costs but also supports sustainability goals by reducing the carbon footprint of refrigeration operations; a vital step towards Net Zero.
2. Proactive Maintenance and Reduced Downtime
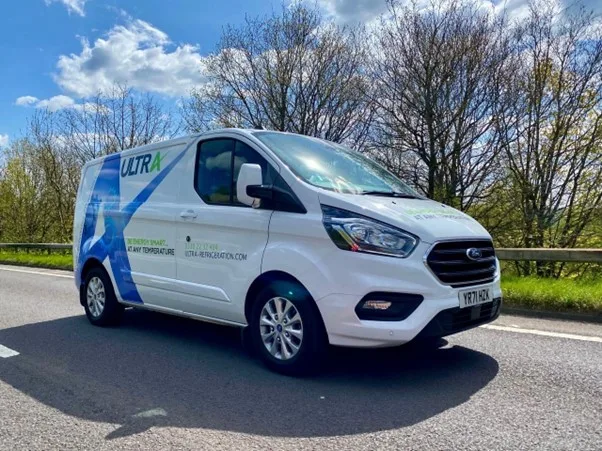
By continuously tracking the performance of refrigeration equipment, management systems can alert operators to potential issues, so they can be fixed before they cause a failure.
This proactive approach reduces costly downtime, which can be especially damaging in industries such as food and pharmaceuticals, where temperature-sensitive goods need to be stored at specific conditions.
In a practical sense, being able to analyse system performance remotely in advance of a visit, helps ensure an engineer brings the right parts and tools to fix the problem that has been identified, saving time and money.
3. Identify Cost Savings
By helping identify issues early, improving energy efficiency, and reducing downtime, advanced controls directly contribute to cost savings.
With the detailed insights provided by such systems, businesses can better understand where they are spending on energy and identify opportunities for optimisation. For example, adjusting temperature settings based on external conditions (free cooling) or scheduling defrost cycles more efficiently can lead to significant reductions in energy consumption.
In one instance, we empirically determined that we could switch off the refrigeration plant on a cold store overnight without adversely affecting the food temperature, leading to significant annual cost savings.
4. Increased Security and Compliance
In industries where strict regulations govern temperature and humidity (such as food safety and pharmaceutical storage), the data collected in the control system plays a crucial role in ensuring compliance. Continuous tracking of performance can be used to generate reports that help prove businesses are compliant with relevant standards and health and safety regulations, avoiding potentially costly fines.
5. Enhanced Data Insights for Control and Strategic Decisions
Advanced management systems provide businesses with a level of visibility and control that would be impossible through on-site, hands-on management alone. Operators can remotely monitor multiple refrigeration units across various sites, whether they are in a single facility or located across the country. This centralised control makes it easier to spot trends, track and compare energy usage, and quickly identify problems across the entire operation.
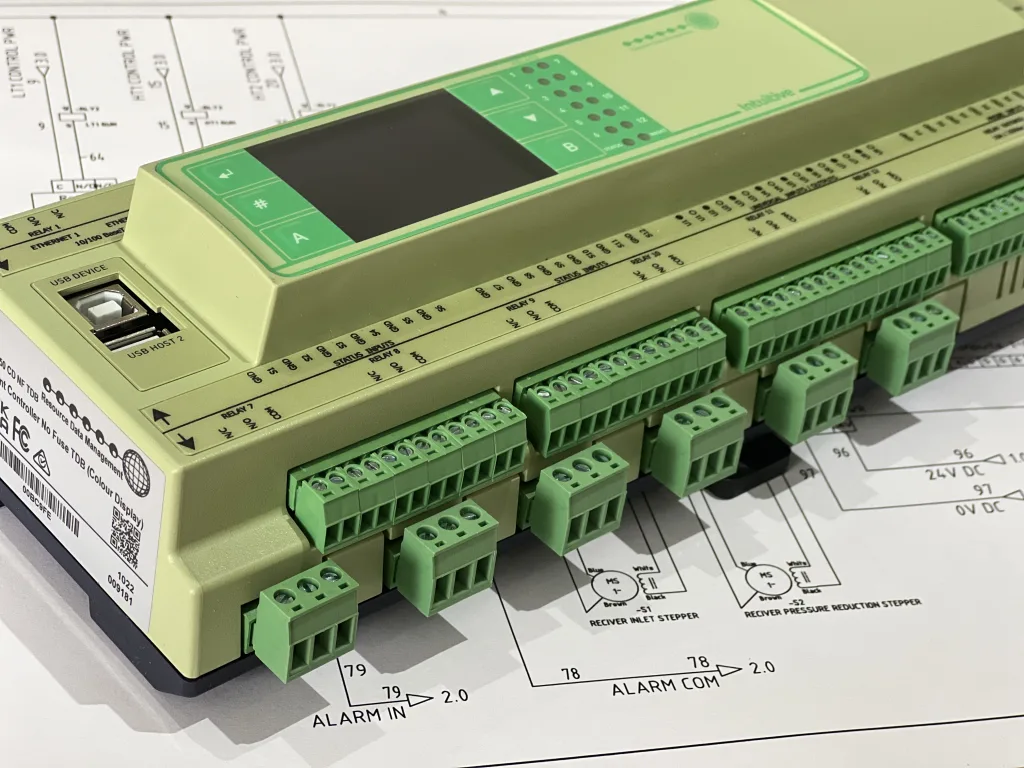
This can also can provide valuable insights for long-term strategic planning. By analysing trends in system performance, energy usage, and maintenance, businesses can make informed decisions about equipment upgrades, replacements, and capacity planning.
For instance, if a certain system frequently requires repairs or consumes more energy than similar units, it may be time to consider an upgrade to more efficient equipment. Additionally, operators can use data to plan maintenance schedules more effectively, helping to extend the life of their refrigeration assets and improve return on investment.
6. Peace of Mind
Knowing that refrigeration systems are being continuously monitored and are operating as efficiently as possible provides peace of mind to business owners, managers, and staff. Whether it’s ensuring that sensitive products like vaccines, perishable foods, or chemicals are being stored correctly, advanced management controls provide an added layer of reassurance that systems are functioning as they should.
With remote monitoring providing the ability to access the system’s status from anywhere, operators no longer need to be physically present to make informed decisions or act on potential issues.
Conclusion
The benefits of advanced management controls for refrigeration systems are clear. From improved performance, proactive maintenance to cost savings, regulatory compliance, and improved control, these controls are transforming how businesses manage their refrigeration assets. As these controls continue to evolve, through technology advances, software and the use of AI, their role will only grow in importance, helping businesses stay competitive, reduce risks, and deliver greater value to their customers.
If you’d like to discuss ways of incorporating advanced controls into a new system or improving the efficiency of your existing refrigeration equipment, or want to talk about a new project, please get in touch by emailing us today at info@ultraref.co.uk or calling us on +44 (0) 330 2232404.